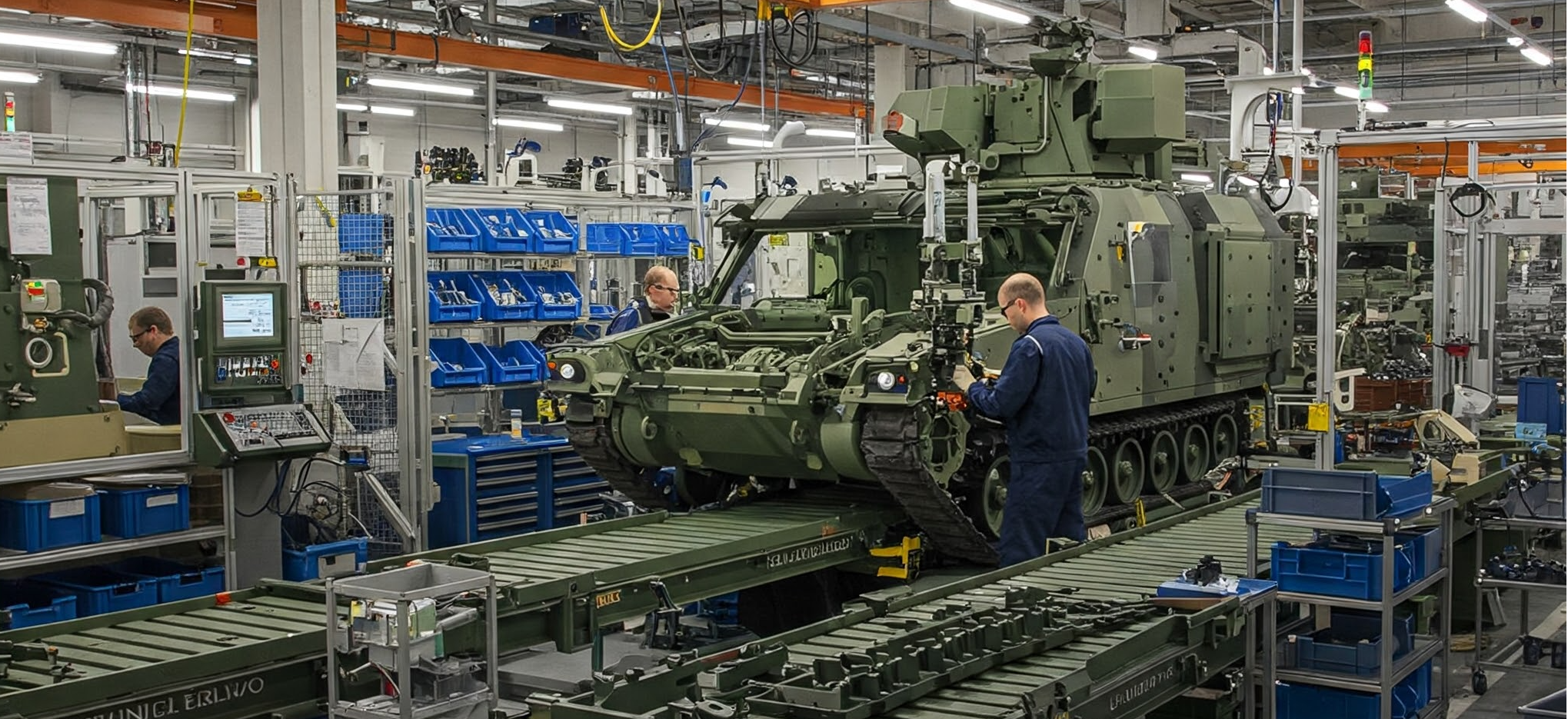
In today's dynamic landscape, particularly within the critical realm of defense manufacturing, clinging to outdated production methodologies is not just inefficient – it's a strategic liability. As a systems expert in manufacturing production, I've witnessed firsthand the transformative power of modern technology, and it's clear: for the defense industry, embracing manufacturing intelligence services is no longer a competitive advantage, it's a fundamental requirement for survival and success.
Consider the stakes. Whether it's peacetime readiness or wartime surge capacity, the defense sector operates under unparalleled pressure to deliver quality products, on time, and within budget. Failure can have profound consequences, impacting national security and the lives of those who serve. In this environment, can you afford production bottlenecks, unexpected downtime, or quality deviations? The answer, unequivocally, is no.
This is where the power of Industry 4.0 technologies comes into sharp focus. We're talking about more than just buzzwords; we're talking about tangible tools that provide a non-negotiable edge in defense manufacturing operations.
The Industry 4.0 Advantage for Defense Manufacturing
Real-time Data Analytics:
The ability to determine precise health and performance of every machine on your factory floor, in real time, is a superpower for the manufacturing plant management. This isn't science fiction; it's the reality enabled by modern production analytics. By continuously monitoring key performance indicators (KPIs), you gain immediate insights into operational efficiency, identify potential bottlenecks before they escalate, and make data-driven decisions that optimize output.
Predictive Maintenance:
Reactive maintenance is a costly gamble. Waiting for equipment to fail leads to unplanned downtime, rushed repairs, and potential delays in critical deliveries. Predictive maintenance, powered by sophisticated algorithms and machine learning, analyzes historical and real-time data to forecast potential equipment failures. This allows for proactive interventions, minimizing disruptions, extending asset life, and ultimately ensuring consistent production flow.
Digital Twins:
Creating virtual replicas of your production assets and processes – digital twins – offers an unprecedented opportunity for simulation, optimization, and training. Before implementing changes on the physical shop floor, you can test scenarios, identify potential issues, and fine-tune processes in a virtual environment. This reduces risk, accelerates innovation, and enhances overall efficiency.
Production Analytics:
Beyond real-time monitoring, comprehensive production analytics provides a holistic view of your entire manufacturing ecosystem. By analyzing historical trends, identifying patterns, and benchmarking performance, you can unlock hidden efficiencies, optimize resource allocation, and continuously improve your production processes.
Strategic Implications for Defense Manufacturing
For the defense industry, the implications are profound. Imagine:
- Enhanced Readiness: Proactive maintenance ensures that critical equipment is always operational, maximizing readiness and minimizing delays in deployment.
- Increased Efficiency: Optimized production processes and reduced downtime translate directly into higher output and lower costs – crucial for managing tight defense budgets.
- Improved Quality: Real-time monitoring and predictive analytics contribute to tighter quality control, minimizing defects and ensuring the reliability of mission-critical equipment.
- Agile Response to Demand Fluctuations: During wartime or periods of increased demand, the ability to rapidly scale production and adapt to changing requirements is paramount. Modern technology provides the agility needed to meet these challenges effectively.
The era of relying on manual processes and reactive measures is over. The defense industry demands a proactive, data-driven approach to manufacturing. By embracing Industry 4.0 technologies and partnering with experts who offer advanced manufacturing intelligence services, defense manufacturers can achieve the unnegotiable edge needed to meet today's challenges and secure tomorrow's success.
Are you ready to future-proof your defense production capabilities? The time to act is now.
Ready to Modernize Your Defense Manufacturing?
Our team of experts can help you implement Industry 4.0 technologies and processes needed to achieve and maintain war-time readiness for your defense manufacturing operations.